Unleashing Business Potential Through Advanced Bulk Material Handling Solutions
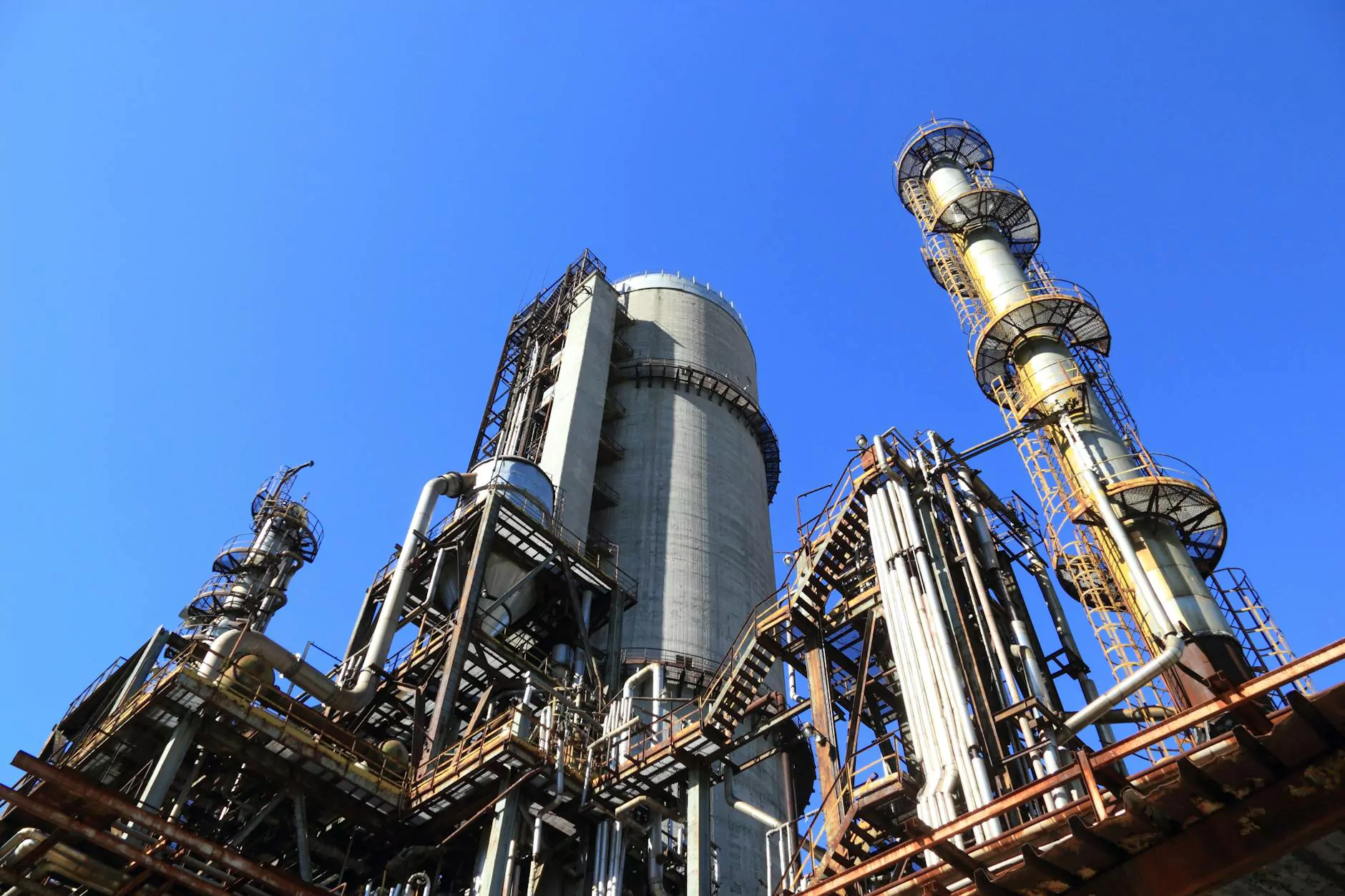
In today’s rapidly evolving industrial landscape, the efficiency and safety of bulk material handling operations have become central to the success of manufacturing, logistics, and technological enterprises. The integration of cutting-edge technology, innovative engineering, and tailored solutions has transformed traditional methods into streamlined, cost-effective systems. This comprehensive guide explores how bulk material handling influences business growth, highlights the synergy with sectors such as electronics and 3D printing, and provides strategic insights to optimize your operations.
Understanding the Significance of Bulk Material Handling in Modern Industry
Bulk material handling encompasses the collection, storage, retrieval, and transportation of large quantities of raw materials or finished products. Whether dealing with powders, granules, or large components, efficient handling systems are vital for maintaining productivity and minimizing operational costs.
Key Benefits of Effective Bulk Material Handling
- Increased Productivity: Automated systems enable faster processing times and reduce manual labor.
- Cost Efficiency: Optimized flow reduces waste, downtime, and energy consumption.
- Enhanced Safety: Modern handling systems minimize workplace accidents and material spillage.
- Quality Control: Proper handling preserves material integrity and consistency.
- Flexibility and Scalability: Adaptable systems can grow with your business demands.
The Evolution of Bulk Material Handling: From Traditional to Advanced Systems
The genesis of bulk material handling was rooted in manual processes, which posed significant challenges due to labor intensity, safety concerns, and inefficiency. The advent of mechanized systems—such as belt conveyors, screw feeders, and pneumatic conveying—marked a turning point. Today, the integration of digital automation, IoT sensors, and AI optimizes these systems further, providing real-time data analytics and predictive maintenance capabilities.
Leading companies like polygonmach.com exemplify innovation in bulk material handling, offering customized solutions tailored to diverse industrial needs, including electronics manufacturing and 3D printing sectors.
The Role of Bulk Material Handling in Electronics Manufacturing
The electronics industry relies heavily on precise and contamination-free handling of small, sensitive components such as microchips, resistors, and capacitors. Efficient bulk material handling systems facilitate the seamless movement, storage, and distribution of these components, ensuring high-quality assembly processes.
Modern handling solutions in electronics manufacturing incorporate cleanroom-compatible conveyors, vibratory feeders, and automated storage/retrieval systems. These innovations help prevent dust and static build-up, preserving component integrity and compliance with stringent industry standards.
Impact on Production Efficiency and Quality Control
Advanced bulk material handling significantly reduces manual handling errors, ensures faster throughput, and maintains the precision needed for complex electronic assemblies. Real-time monitoring and control systems also enable immediate response to any anomalies, preventing costly delays or defects.
Transforming 3D Printing Through Innovative Material Handling
As 3D printing gains popularity across diverse sectors—from aerospace to healthcare—efficient handling of printing materials becomes increasingly critical. Bulk material handling solutions optimized for powders, filaments, and resins contribute directly to improved print quality, process reproducibility, and operational scalability.
Industrial-grade hoppers, automated dispensing systems, and closed-loop circulation equipment—integrated with the printing machinery—ensure consistent material flow and minimize waste. Such systems also facilitate safe handling of potentially hazardous or specialized materials.
Key Technologies Supporting 3D Printing Material Handling
- Automated Feeders and Dispensers: Maintain precise flow control for high-quality prints.
- Vibration and Agitation Systems: Prevent material settling or clumping in storage containers.
- Filament and Powder Storage Solutions: Ensure contamination-free, controlled environments for sensitive materials.
- Conveyor and Supply Systems: Streamline material transfer from storage to printer, reducing manual intervention.
How to Choose the Right Bulk Material Handling System for Your Business
Selecting the ideal system requires thorough assessment of your operational needs, material characteristics, and future growth plans. Here are essential factors to consider:
- Material Properties: Particle size, flowability, abrasiveness, moisture sensitivity, static charge potential.
- Capacity and Throughput: Volume of material to be handled daily or periodically.
- System Compatibility: Integration with existing machinery, automation levels, and spatial constraints.
- Safety and Regulatory Compliance: Handling hazardous materials, dust containment, static control, and environmental regulations.
- Scalability and Flexibility: Ability to adapt to future changes in product lines or processing volume.
- Cost and Maintenance: Initial investment, operational costs, ease of maintenance, and long-term durability.
Innovative Bulk Material Handling Technologies by Polygonmach
Polygonmach stands at the forefront of delivering bespoke bulk material handling equipment, tailored specifically to industry requirements. Their forward-thinking solutions encompass a range of technologies including automated conveyor systems, pneumatic transfer lines, and integrated control platforms.
Their commitment to quality and innovation ensures that businesses in electronics, 3D printing, and other manufacturing sectors gain a competitive edge through improved efficiency, safety, and sustainability.
Future Trends in Bulk Material Handling and Business Growth
The future of bulk material handling lies in integrating smart systems, IoT connectivity, and AI-driven analytics. These advancements offer predictive maintenance, real-time process optimization, and extensive data collection, enabling businesses to make informed decisions and reduce downtime.
Furthermore, environmentally conscious practices such as energy-efficient equipment, waste reduction strategies, and material recycling are gaining importance, aligning business goals with sustainable development principles.
Maximizing Business Success with Comprehensive Bulk Material Handling Strategies
Optimizing bulk material handling is not solely about selecting the right machinery but involves strategic planning, process integration, and ongoing evaluation. Adopting a holistic approach ensures maximum throughput, minimal downtime, and superior product quality.
Key steps include:
- Conducting a thorough material analysis and process review.
- Designing custom handling solutions aligned with operational goals.
- Implementing automation and control systems for real-time monitoring.
- Providing staff training to ensure safe and efficient operation.
- Scheduling regular maintenance and system audits.
- Leveraging industry innovations and technological upgrades.
Conclusion: Embracing Innovation to Elevate Business in Bulk Material Handling
The landscape of bulk material handling is dynamic, with technological innovations continuously pushing the boundaries of efficiency and safety. By integrating advanced systems, embracing automation, and collaborating with industry leaders like polygonmach.com, businesses can unlock new levels of productivity and competitiveness.
Whether operating in electronics manufacturing, 3D printing, or other sectors reliant on bulk material logistics, understanding and investing in the right handling solutions are crucial steps toward sustained growth and industry leadership.