Transforming Industries: The Role of Industrial Blade Factories
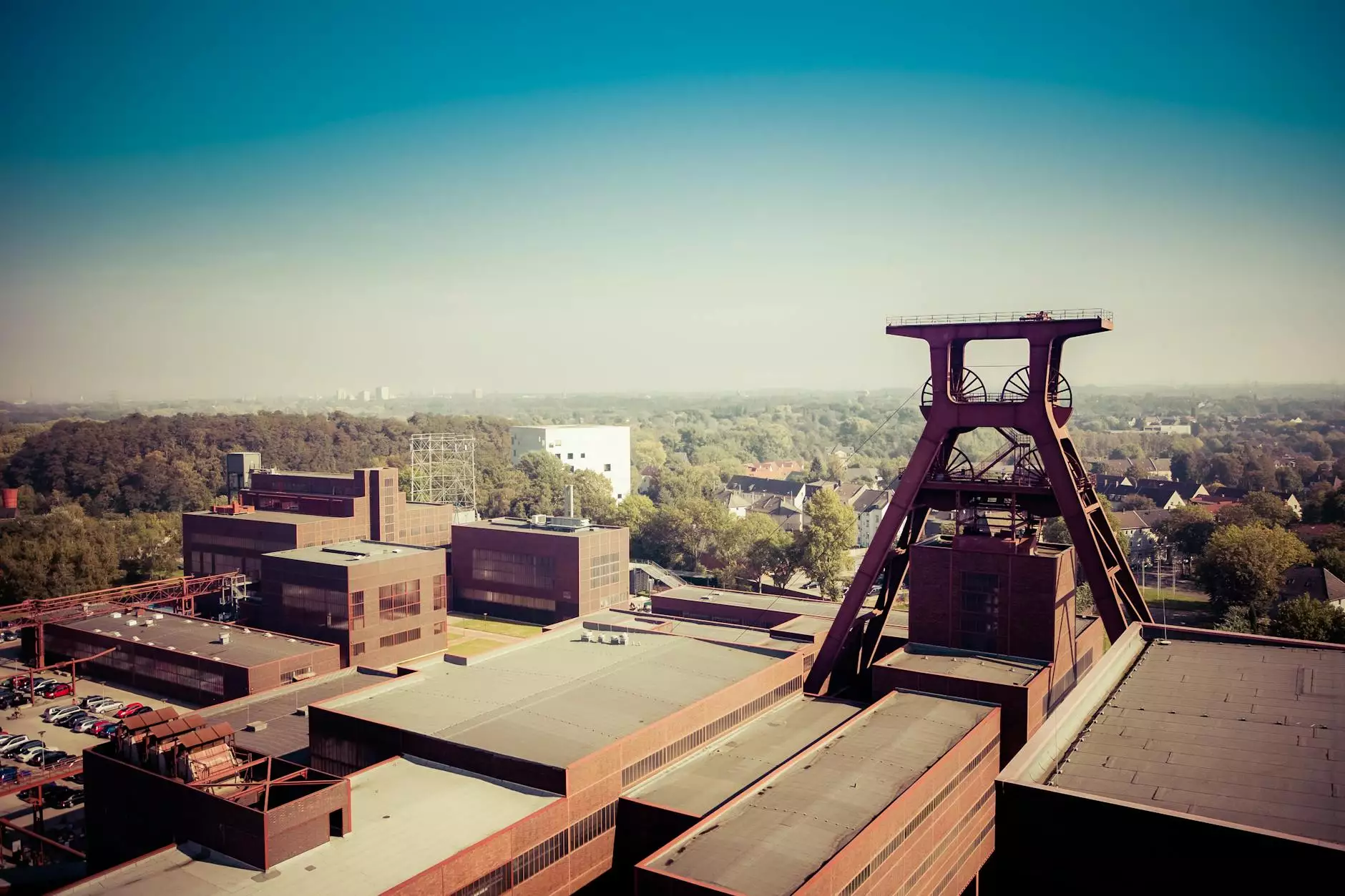
In today's competitive market, industrial blade factories play a pivotal role in enhancing the efficiency and productivity of various sectors. As businesses strive for superior quality and precision in their operations, the demand for high-quality blades and cutting tools continues to soar. This article delves into the significance of industrial blade factories, focusing on the professional services they provide, particularly in the realm of knife sharpening.
The Importance of Industrial Blade Factories
Industrial blade factories are specialized manufacturing facilities that produce a variety of cutting tools and blades used across multiple industries, including woodworking, metalworking, food processing, and more. The prominence of these factories in the modern industrial landscape cannot be overstated, and here’s why:
- Quality Materials: Industrial blade factories often utilize high-grade materials that enhance the durability and performance of cutting tools.
- Precision Engineering: With advanced technology and skilled engineers, these factories ensure that blades are manufactured to exact specifications, reducing waste and improving cut quality.
- Customized Solutions: Many industrial blade manufacturers offer tailored blade solutions to meet specific client needs, which is indispensable in industries with unique cutting requirements.
- Efficiency in Production: These factories implement innovative production methods that streamline manufacturing processes, resulting in faster turnaround times and cost savings.
Knife Sharpening: A Vital Professional Service
One of the essential services provided by industrial blade factories is knife sharpening. In industries where precision cutting is fundamental, maintaining the sharpness of knives and blades is crucial. Here’s how professional knife sharpening contributes to operational excellence:
Enhancing Performance
A sharp knife performs better—it cuts through materials with ease and precision. Dull blades can lead to:
- Increased Downtime: Workers often need to stop to replace dull blades, which can significantly hinder productivity.
- Poor Quality Cuts: Dull blades can produce jagged or uneven cuts, leading to compromised product quality.
- Safety Risks: Using dull knives can increase the likelihood of accidents as users apply more force, which can lead to slips and injuries.
Cost-effectiveness
Regular knife sharpening services provided by industrial blade factories can greatly reduce the overall costs associated with blade replacement. By extending the lifespan of blades, businesses can allocate resources more efficiently. Here’s how:
- Reduced Replacement Costs: Quality sharpening can make blades last significantly longer, thereby minimizing the frequency of replacements.
- Better Production Rates: Well-maintained tools contribute to smoother workflows, directly impacting overall productivity and profit margins.
Professional Expertise
Industrial blade factories often employ skilled technicians who have extensive knowledge and experience in blade maintenance. Their expertise ensures:
- Optimal Sharpening Techniques: Different types of blades require specific sharpening methods; professional services cater to these unique requirements.
- Assessment of Blade Condition: Technicians can determine the viability of a blade and whether it requires sharpening or complete replacement.
The Technological Edge in Blade Production
Modern industrial blade factories leverage cutting-edge technology to enhance manufacturing processes and product quality. Some of the notable advancements include:
Automation and Robotics
Many factories adopt automated systems to increase production efficiency. Robotics help in:
- Consistent Quality: Automation ensures that each blade produced meets stringent quality standards.
- Reduced Labor Costs: An automated workforce can operate with fewer human resources, leading to lower operational costs.
High-Precision Machining
Modern machining techniques allow for precise cuts and shaping of blades. CNC (Computer Numerical Control) machines are frequently used to:
- Minimize Human Errors: Automated machines ensure accuracy in production, which is vital in blade manufacturing.
- Enhance Design Flexibility: CNC technology allows for rapid prototyping and the creation of custom designs quickly and efficiently.
Environmental Responsibility in Blade Manufacturing
As industries worldwide strive to adopt sustainable practices, industrial blade factories are also adapting to these changes. Emphasizing environmental responsibility is becoming increasingly important. Here's how:
Sustainable Material Use
Many manufacturers are shifting towards eco-friendly materials and production methods. They prioritize:
- Recycled Materials: Using recycled steel and other materials helps reduce waste and energy consumption.
- Minimizing Waste: Advanced cutting techniques reduce excess material waste during the manufacturing process.
Energy-efficient Production Processes
Innovative manufacturing processes in industrial blade factories often focus on reducing energy consumption. Examples include:
- Energy-efficient Machines: Investing in equipment that consumes less power while maintaining production levels.
- Alternative Energy Sources: Utilizing solar and wind power to supplement traditional energy sources in factories.
Future Trends in the Industrial Blade Manufacturing Industry
The industrial blade manufacturing landscape is continually evolving, driven by advancements in technology and changes in consumer demands. Here are some future trends to watch:
Smart Manufacturing
The integration of IoT (Internet of Things) into manufacturing processes is set to revolutionize the industry. Key advantages include:
- Real-time Monitoring: Machines can report their status and performance, leading to timely maintenance and reduced downtime.
- Data-Driven Decisions: Analyzing data collected from machines can optimize production processes and improve product quality.
Customized Production
As businesses seek more personalized solutions, industrial blade factories will increasingly focus on customization. This involves:
- Client Collaborations: Working closely with clients to develop tailored products that meet specific operational needs.
- Flexible Manufacturing Systems: Adopting systems that can easily adapt to changes in production requirements.
Conclusion
In conclusion, industrial blade factories are essential components of modern industry. They provide invaluable services, particularly in knife sharpening, contributing to operational efficiency, cost savings, and enhanced safety. By embracing advanced technologies and sustainable practices, these factories not only improve their production capabilities but also ensure environmental responsibility. As the industry evolves, the adaptability and responsiveness of industrial blade factories will be critical in meeting the ever-changing demands of various sectors.
For businesses looking to enhance their cutting tool performance, investing in the services offered by an established industrial blade factory like SZBlade.com is a strategic step towards achieving operational excellence. Their commitment to quality and innovation positions them as a leader in the industry, making them a top choice for professional services.