Understanding Pressure Vessel Regulations for Safe Operations
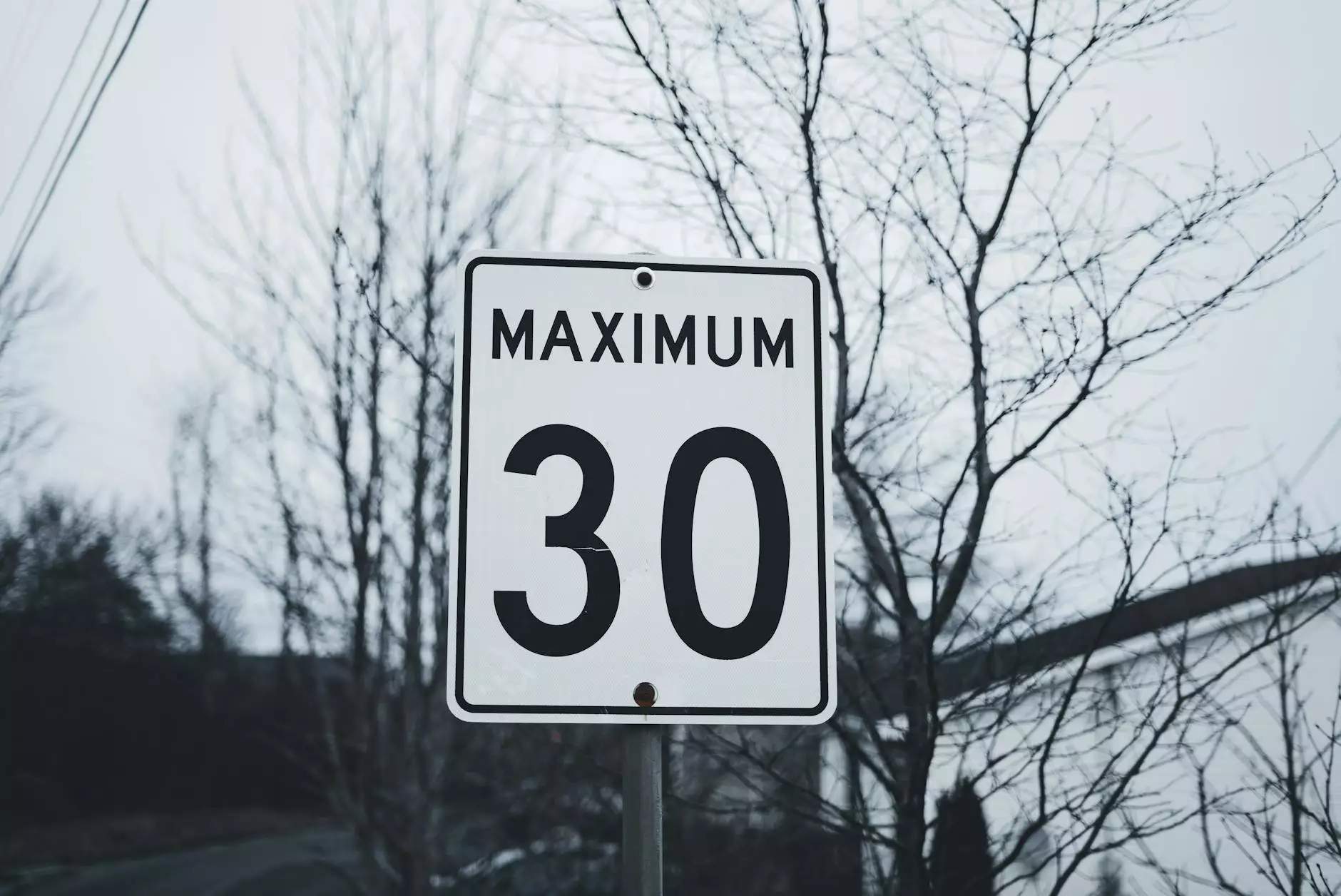
In industries that utilize high pressure and temperature systems, pressure vessels are crucial components that demand rigorous scrutiny to ensure safe and efficient operations. This article delves into the intricate world of pressure vessel regulations, outlining the definitions, standards, design requirements, inspection protocols, operational guidelines, documentation obligations, and compliance necessities essential for businesses operating within this domain.
1. Definitions of Key Terms
To effectively navigate the complexities of pressure vessel regulations, one must first grasp the essential terminology:
- Pressure Vessel: A container designed to hold gases or liquids at a pressure substantially different from the ambient pressure.
- Design Pressure: The maximum pressure that a pressure vessel is designed to withstand under normal operating conditions.
- Safety Valve: A critical safety device intended to release excess pressure to prevent catastrophic failure.
- Fabrication: The process of constructing a pressure vessel, which involves material selection and manufacturing techniques.
- Non-destructive Testing (NDT): A suite of testing methods used to evaluate the integrity of materials and components without causing damage.
2. Standards and Codes Governing Pressure Vessels
The design, manufacture, and maintenance of pressure vessels are governed by various national and international standards. One of the most prominent is the ASME Boiler and Pressure Vessel Code (BPVC). This code provides comprehensive guidelines for:
- Design and Construction: Establishing criteria for material selection, fabrication processes, and design calculations.
- Inspection and Testing: Outlining mandatory inspections and tests throughout the vessel's lifecycle.
- Repair and Alteration: Standards for safe modifications to pressure vessels that ensure ongoing compliance.
Other relevant regulations include API standards for oil and gas and ISO standards that specify safety measures for various operational scenarios.
3. Designing Pressure Vessels: Essential Requirements
The design phase of a pressure vessel is paramount in ensuring its safety and efficiency. Here are key design requirements:
- Material Selection: The materials used must withstand both internal pressure and corrosive elements, such as acids or bases.
- Structural Integrity: Designers must incorporate safety factors to mitigate risks from unexpected pressure surges.
- Design Calculations: Detailed calculations must verify that the vessel can handle maximum expected pressures and temperatures.
4. Inspection and Testing Protocols
Once a pressure vessel is fabricated, it undergoes stringent inspection and testing to ensure it meets all safety criteria.
4.1 Types of Inspections
Inspections can be categorized as follows:
- Visual Inspection: Checking for physical signs of wear, corrosion, or damage.
- Non-destructive Testing: Methods such as ultrasonic testing, radiography, and magnetic particle testing are employed to assess the internal integrity without damaging the vessel.
4.2 Frequency of Inspections
The frequency of inspections often depends on:
- The material of construction
- The service conditions
- Regulatory requirements
Regular maintenance and inspection logs are instrumental in tracking the vessel's condition over time.
5. Operational Guidelines for Safety
To ensure safe operation, businesses must adhere to specific operational guidelines, which include:
- Maximum Operating Pressure: Operating a pressure vessel above its design pressure can result in failure.
- Temperature Limits: Each vessel must operate within specified temperature limits to prevent structural degradation.
- Control Systems: Implementing robust monitoring systems for pressure and temperature can provide early warnings of potential issues.
6. Comprehensive Documentation Practices
Maintaining meticulous documentation is essential for regulatory compliance:
- Design Calculations: These must be archived as evidence of compliance with design pressure and material requirements.
- Inspection Reports: Detailed records of inspections and tests must be maintained to verify ongoing safety and compliance.
- Maintenance Logs: Documenting maintenance actions can help identify patterns that may indicate potential issues in the future.
7. Compliance and Enforcement
Understanding the compliance landscape is critical for any business managing pressure vessels. Key points include:
- Regulatory Bodies: Agencies such as the Health and Safety Executive (HSE) in the UK are pivotal in enforcing safety regulations and standards.
- Compliance Obligations: Businesses must familiarize themselves with the relevant codes and ensure all practices align with established regulations.
- Penalties for Noncompliance: Failure to adhere to safety regulations can result in severe penalties, including fines and operational shutdowns, underscoring the importance of compliance.
8. Conclusion
The importance of pressure vessel regulations cannot be overstated in safeguarding both personnel and assets in industrial settings. By adhering to established standards, conducting regular inspections, maintaining robust documentation, and ensuring compliance with relevant regulations, businesses can promote a culture of safety and efficiency.
Through diligent efforts in understanding and implementing these regulations, companies can not only protect their investments but also build a reputation for reliability and safety in their operations. By prioritizing the highest standards in pressure vessel management, businesses can navigate the complexities of their industries with confidence and integrity.
9. Resources for Further Reading
For those interested in further exploring pressure vessel regulations, a number of invaluable resources are available:
- ASME Codes and Standards
- Health and Safety Executive (HSE)
- API Standards
- International Organization for Standardization (ISO)