Understanding H2S Monitor Calibration: A Comprehensive Guide
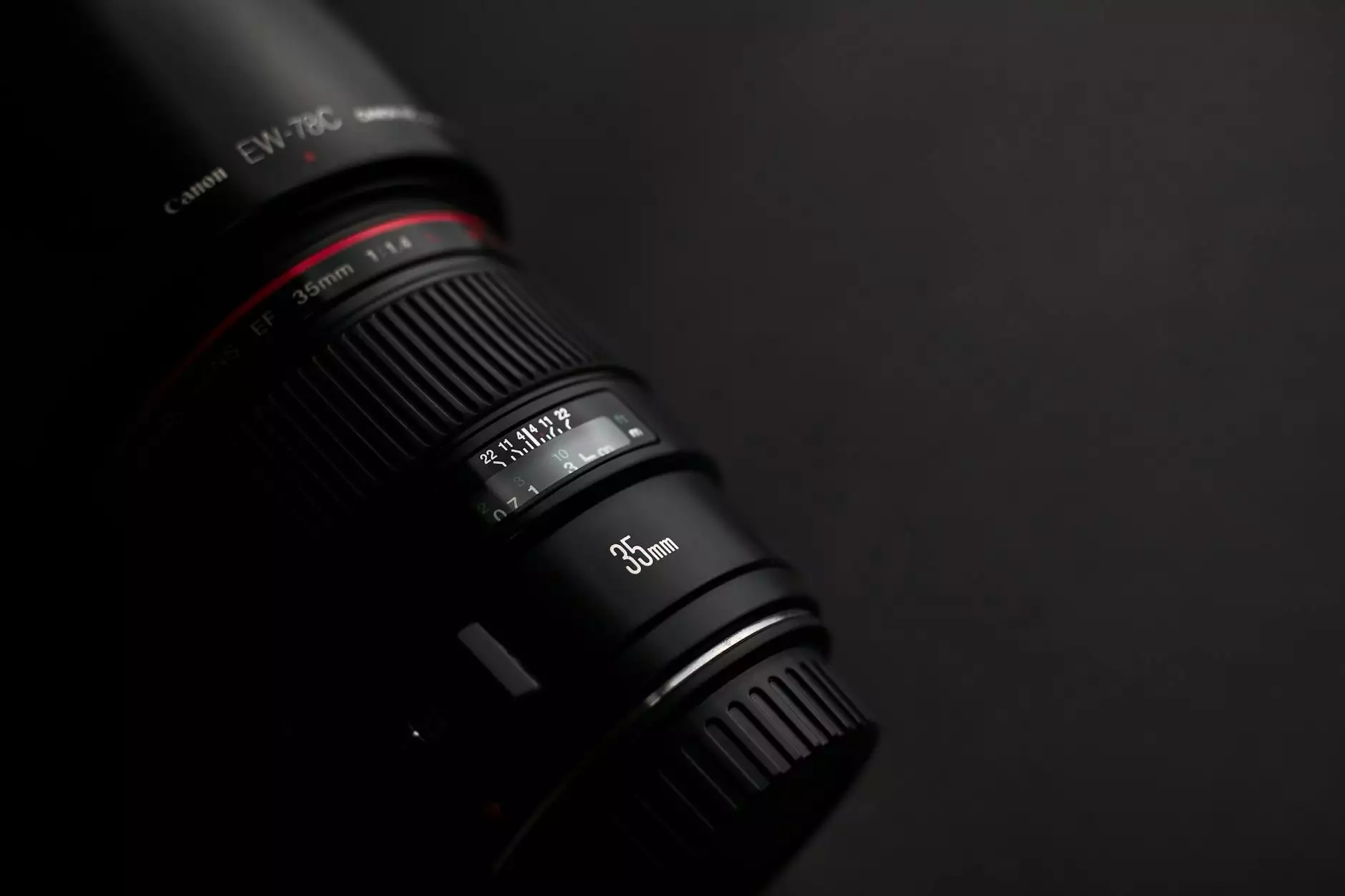
Introduction to H2S Monitors
The safety of workers in industries such as oil and gas, wastewater treatment, and mining is paramount. One of the critical tools utilized in these industries is the H2S monitor, which is designed to detect hydrogen sulfide gas. Accurate measurement and monitoring are essential to ensure safety and compliance with health regulations. This is where H2S monitor calibration comes into play.
The Importance of H2S Monitor Calibration
Calibration is essential for any monitoring device to maintain its accuracy and reliability. The importance of H2S monitor calibration includes the following:
- Precision in Detection: Regular calibration ensures that the device can accurately detect H2S levels, which is crucial for preventing exposure to toxic gases.
- Regulatory Compliance: Many industries are governed by strict safety regulations that require accurate monitoring and calibration of equipment.
- Enhanced Safety: Accurate readings help to mitigate the risk of accidents caused by undetected H2S concentrations.
- Equipment Longevity: Proper calibration can extend the lifespan of H2S monitors and prevent costly replacements.
What is H2S Gas?
Hydrogen sulfide (H2S) is a colorless gas with a characteristic odor of rotten eggs. It is highly toxic and poses serious health risks, including:
- Nausea and Vomiting: Prolonged exposure can cause severe nausea and gastrointestinal issues.
- Respiratory Problems: Higher concentrations of H2S can lead to respiratory distress or failure.
- Long-term Health Effects: Chronic exposure can result in long-term health effects, including neurological damage.
How Does H2S Monitoring Work?
H2S monitors detect the presence of hydrogen sulfide gas using various sensor technologies. The most common types of sensors include:
- Chemical Sensors: Utilize chemical reactions to detect changes in concentration levels.
- Electrochemical Sensors: Measure the current produced by the reaction of H2S with the sensor material.
- Photoionization Sensors: Use ultraviolet light to ionize H2S molecules and measure the electrical response.
Procedures for H2S Monitor Calibration
Calibrating H2S monitors involves several critical steps to ensure accurate readings:
- Gather Necessary Equipment: This includes calibration gas, a regulator, and a calibration cap.
- Prepare the H2S Monitor: Turn on the device and allow it to warm up as per the manufacturer's instructions.
- Set Up Calibration Gas: Attach the calibration gas cylinder to the regulator and set the proper flow rate.
- Expose the Monitor: Connect the calibration cap and expose the monitor to the calibration gas for the specified time.
- Record the Readings: Take note of the readings displayed on the monitor to compare against the expected values.
- Adjust Calibration Settings: If the readings are not within the acceptable range, adjust the calibration settings as per the manufacturer’s guidelines.
- Document the Calibration: Keep a detailed record of the calibration process, including date, time, and results for compliance purposes.
Best Practices for H2S Monitor Calibration
To ensure effective calibration and ongoing performance of H2S monitors, consider the following best practices:
- Regular Calibration: Schedule calibration at regular intervals, typically every 6 months, or as recommended by the manufacturer.
- Environmental Considerations: Ensure that the calibration is performed in an environment similar to where the monitor will be used.
- Use Certified Calibration Gases: Always use calibration gases that are certified to ensure accuracy in your readings.
- Training and Certification: Ensure that personnel conducting the calibration are properly trained and certified to perform these tasks.
- Backup Systems: Utilize additional safety measures, such as backup monitors, to ensure continuous protection.
Common Issues Encountered During Calibration
During the calibration process, you may encounter several issues, including:
- Drift in Sensor Readings: Sensors can drift over time, leading to inaccurate readings. Regular checks can help mitigate this.
- Contaminated Calibration Gases: Using contaminated gases can produce false readings; ensure gases are stored properly.
- Inadequate Sensor Response Time: Ensure your sensors are responsive enough to detect changes in H2S levels quickly.
The Role of Educational Services in H2S Monitor Calibration
With the increasing necessity for compliance and safety in workplaces handling hazardous materials, educational services play a vital role in ensuring personnel are adequately trained in the calibration of H2S monitors. The benefits of educational services include:
- Skill Development: Training programs enhance the skills and knowledge of workers, making them more effective in their roles.
- Health and Safety Protocols: Educational services provide critical information on health and safety procedures and regulations.
- Hands-On Experience: Practical training ensures that workers feel confident in using and calibrating H2S monitors.
Conclusion
H2S monitor calibration is an essential aspect of workplace safety in industries dealing with hazardous gases. By understanding the importance of calibration, the process involved, and the best practices to follow, organizations can enhance their safety measures and ensure compliance with regulations. Investing in thorough training and educational services can further solidify a company’s commitment to safety and the well-being of its employees. Remember, regular calibration is not just a requirement; it is a crucial aspect of ensuring a safe working environment.
Get Started with Your H2S Monitor Calibration Today
For those looking to delve deeper into H2S monitor calibration and ensure that their workplace remains safe, contact H2S Online Training for expert-led training programs and resources that can empower you and your team with the necessary knowledge and skills.